COM_SPPAGEBUILDER_NO_ITEMS_FOUND
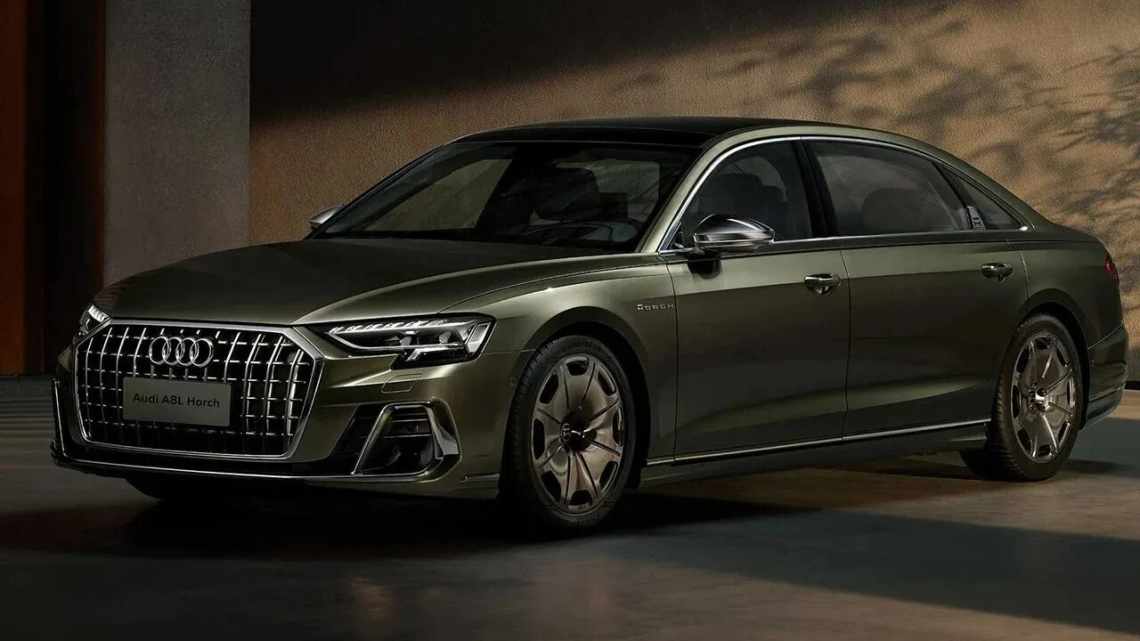
Технократия: тест Audi A8
Audi A8 нового поколения претендует на звание самого высокотехнологичного представительского седана. Так ли это на самом деле? Пытаемся разобраться.
Интересно, но первый флагманский седан компании «Ауди» назывался не А8, а V8 — так прямолинейно немцы намекнули на мотор под капотом. Он вышел на рынок в 1988 году и был построен на растянутой платформе модели Audi 100. В 1994 году дебютировала А8 первого поколения серии D2, спроектированная уже на собственной платформе. Силовая структура его кузова представляла собой пространственную алюминиевую раму Audi Space Frame, а все кузовные панели тоже были сделаны из алюминия — впервые не только в представительском классе, но и в истории массового автопрома! Разумеется, это обеспечило «авоське» существенное преимущество в массе перед конкурентами — кузов весил всего 249 килограммов.
Когда-то и у меня был такой автомобиль, с 4,2-литровым мотором V8 мощностью 300 лошадиных сил — разумеется, на полном приводе quattro. Он очень напористо разгонялся, здорово ехал и я до сих пор помню эту фирменную эмблему ASF на средней стойке кузова — алюминий тогда стал настоящей визитной карточкой Audi. Следующее поколение А8 дебютировало в 2003 году: седан серии D3 остался верен традициям и был так же построен на пространственной раме Audi Space Frame с кузовными панелями из алюминия. Но его кузов стал ещё легче: всего 220 килограммов!
А вот кузов третьего поколения флагмана серии D4, которое увидело свет в 2009 году, внезапно потяжелел до 231 кг. Виноватой в этом оказалась средняя стойка, в угоду безопасности сделанная из высокопрочной стали. Зато она же обеспечила кузову существенную прибавку в прочности — он стал на 25% жёстче, но алюминия в конструкции осталось лишь 92%. Автомобиль был построен на модульной платформе MLB и подрос в габаритах по сравнению с предшественником. Наконец, в прошлом году дебютировало четвёртое поколение А8 серии D5, кузов которого стал ещё тяжелее — 281 килограмм, а алюминия в нём осталось всего 58%! Стоп, тогда что же остальное? О, это целый ассортимент высокотехнологичных материалов: сталь, магний и даже армированный углеволокном пластик.
Каркас пассажирского салона, включая нижнюю часть передней поперечины кузова, пороги дверей, средние стойки и переднюю часть крыши, состоит из стальных компонентов горячей штамповки. Некоторые элементы из листового металла имеют разную толщину, другие компоненты в процессе производства также подвергаются частичной термообработке, что способствует уменьшению массы и повышению прочности. Алюминиевые детали представляют собой отлитые, профилированные или листовые элементы. Прочность на разрыв некоторых термообработанных сплавов составляет более 230 мегапаскалей, предел текучести в испытании на разрыв превышает 180 МПа, а для сплавов профилей – 280 и 320 МПа, что существенно больше по сравнению с ранее использовавшимися материалами.
Самыми крупными литыми деталями являются соединительные элементы порогов дверей и задние лонжероны, при этом исключительно сложная геометрия, недоступная для обычной стали, позволила увеличить их длину. Растяжка в моторном отсеке изготовлена из магния и весит на 28% меньше, при этом опоры растяжки соединены с кузовом алюминиевыми болтами. При сборке композитной конструкции кузова используется 14 различных методов соединения, включая завальцовку порогов дверей. Данная технология применяется для соединения алюминиевых боковин кузова со стальными листами, полученными методом горячей штамповки, на средней стойке, линии крыши и порогах. Кроме того, она позволяет получать очень узкие фланцы.
Модуль задней стенки из армированного углеволокном пластика, уже оснащённый всеми необходимыми элементами, такими как динамики., шторка и ремни безопасности, монтируется на этапе окончательной сборки: робот устанавливает его в автомобиль через проём заднего стекла. С помощью заклёпок и клея, предотвращающего контактную коррозию, модуль прикрепляется к металлической пространственной раме ASF. По жёсткости на кручение новая Audi A8 превосходит предшественника на 24%, хотя седан стал на 37 миллиметров длиннее, на 13 мм выше и на 4 мм ниже предыдущей модели. Колёсная база подросла на 6 мм, а модель с удлинённой колёсной базой стала длиннее на 130 мм и на 15 мм выше. Кузов собирается при помощи восьми видов сварки, нескольких десятков типов заклёпок, особых саморезов с полимерной изоляцией, специального клея, тиснения и даже пуклёвки.