COM_SPPAGEBUILDER_NO_ITEMS_FOUND
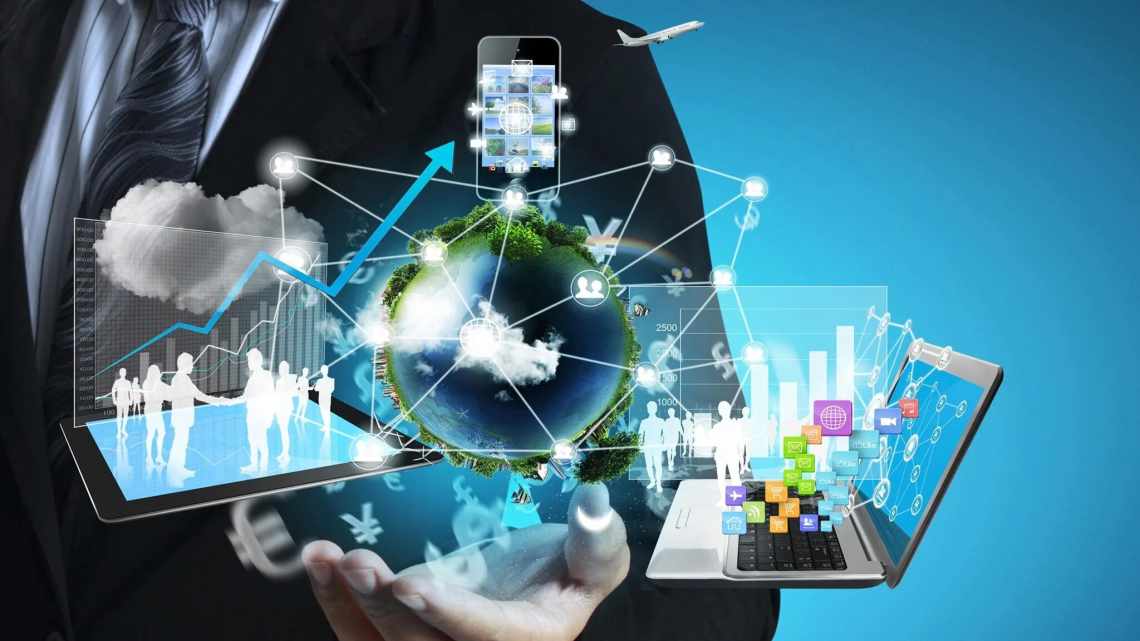
Эпоха цифровых моделей: что сменило циркуль и бумагу в XXI веке
Кульман, циркуль и готовальня — предметы, которые многие из нас использовали на школьных уроках, — в реальности давно ушли в прошлое вместе с «бумажным» проектированием. Уже в 90-е чертежи создавались в компьютерных программах, в нулевых их сменили 3D-модели, а сейчас в истории цифрового моделирования наступает новый этап — виртуальные прототипы начинают «жить» вместе со своими реальными двойниками.
Конструирование виртуального прототипа становится все сложнее: мы пока не дошли до массового применения голограмм и дополненной реальности, чтобы модель будущего изделия можно было буквально обойти со всех сторон и изучить «вживую» — однако новые технологии уже дали проектированию многие другие интересные возможности.
Виртуальный циркуль
Сегодня цифровое проектирование — база для создания самых разных объектов: от жилых зданий до турбин и космических кораблей. Термин «цифровое» означает не просто перенос чертежа с бумаги на экран компьютера: создание моделей сегодня строится на абсолютно новых принципах. Во-первых, к виртуальному макету привязывается вся документация, которая появляется в процессе подготовки производства. Это дает возможность видеть всю хронологию проектирования, включая этапы согласования, любые изменения, заключения и оценки.
Во-вторых, цифровой прототип обычно собирается в 3D-формате, что позволяет сделать расчеты максимально точными. В-третьих, «сборка» модели происходит в режиме реального времени, по технологии нисходящего одновременного проектирования. Это значит, что каждый, кто занимается разработкой макета, видит результаты работы других участников проекта. Это помогает минимизировать риск несостыковок, когда, например, конструктор планирует установку сенсоров на определенном участке оборудования, в то время как его коллега уже отвел этот участок под другой механизм.
И, разумеется, перевод проектирования на цифровые рельсы существенно снизил временные затраты. Так, рабочий проект одной из турбин Уральского турбинного завода, состоящей из 24 тысяч деталей, благодаря внедрению технологии «цифрового макета изделия» сегодня выполняется за 8 месяцев — раньше на эту задачу уходило больше года. А сокращение сроков — это уменьшение издержек и увеличение объема производства. Если ранее на заводе выпускалось от 200 до 300 трехмерных моделей в год — сейчас же это число превратилось в несколько тысяч.
Близнец в цифре
Но хотя цифровая модель решает многие проблемы проектирования, ее жизненный цикл заканчивается с момента появления объекта на свет. Что происходит потом, в период его работы — мы отследить не можем. Иначе говоря, если в процессе создания модели мы еще имеем возможность просчитать, как конечный продукт проявит себя в тех или иных условиях — то все, что будет влиять на его работу после выхода в эксплуатацию, остается темной зоной. А значит, невозможно вовремя выявить нарушения в его работе и предсказать их выход из строя. Во всяком случае, невозможно с помощью «классического» цифрового моделирования: для решения этой задачи необходим полноценный цифровой двойник.
В отличие от цифровой модели, цифровой двойник сохраняет связь со своим реальным воплощением на протяжении всей его жизни — иначе говоря, цифровая модель продолжает существовать и после появления реального объекта, отражая все изменения в его состоянии. Это происходит с помощью технологии промышленного интернета вещей (Industrial Internet Of Things — IIoT): на машинах устанавливаются датчики, которые собирают данные о параметрах их работы и любых изменениях. Например, если датчик «замечает», что в двигателе повысилась температура, давление, уровень вибрации или другой параметр, он передает эти данные в виртуальную модель. На этой модели операторы видят неисправность и могут просчитать, как она повлияет на работу системы, если ее вовремя не исправить.
Это одно из важнейших свойств цифровых двойников: с их помощью можно моделировать различные производственные ситуации и проверять гипотезы — вместо того, чтобы сразу проводить «натурный» эксперимент и рисковать, если что-то пойдет не так. Именно поэтому цифровые двойники имеют столь большой потенциал и в медицине: когда мы научимся воспроизводить работу человеческих органов, мы сможем проверять, как повлияет на них конкретный препарат или хирургическая операция — и уже по результатам экспериментов подбирать подходящее лечение.
Цена ошибки
Но если в медицине цифровые двойники пока остаются делом будущего, в промышленности они уже сегодня помогают экономить огромные средства на износе и авариях оборудования. Благодаря этой технологии предприятия могут вовремя замечать любые неисправности в работе производственных систем и прогнозировать сбои до того, как что-то выйдет из строя. Это критично для промышленных компаний, где даже небольшой простой из-за поломки оборудования может обернуться огромными убытками. Как посчитали в Schneider Electric, в нефтегазовой отрасли решение самой простой проблемы с оборудованием требует не менее трех дней, каждый из которых может «стоить» до $20 тысяч. Но если говорить о внеплановом останове энергоагрегата или тем более последствиях аварии на электростанции, то цифры могут оказаться на порядки выше.
Это приводит к необходимости разработки предиктивных систем на основе технологии цифровых двойников, которые помогают вовремя фиксировать нарушения в работе оборудования. Одно из таких решений, индустриальная IIoT-система «Прана», разработанная РОТЕК, позволяет снизить расходы на ремонт до 60% и, в некоторых случаях, рыночные штрафы. Система состоит из нескольких уровней: нижний передает сигналы с датчиков, далее анализируется информация о режиме работы агрегата. На следующей ступени эти данные передаются в аналитический центр, где математический аппарат системы анализирует их и помогает экспертам обработать данные об отклонениях и сформировать рекомендации для персонала электростанции или другого промышленного предприятия, подключенного к системе.